
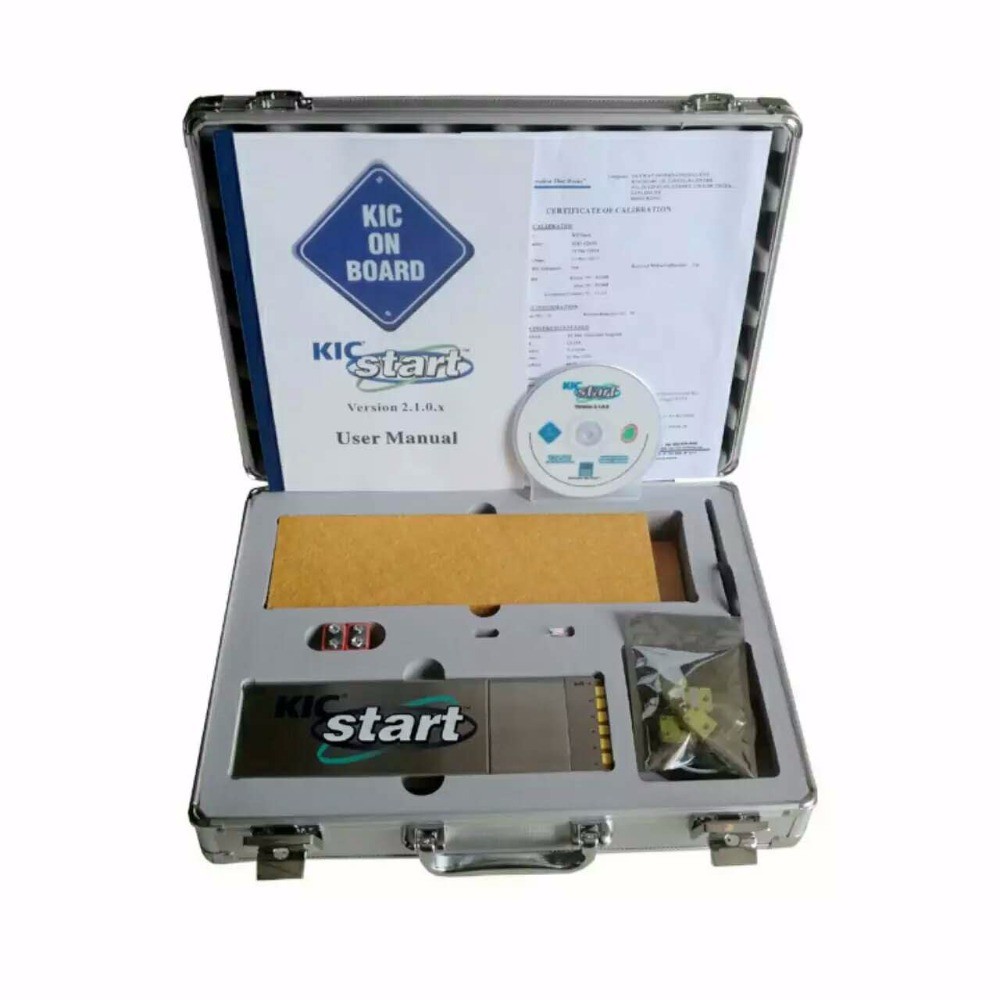
Ideally, the OEM will have provided their assembly partner with a populated printed circuit assembly. Using their skill, judgement and experience, the NPI engineer will select the profile and temperature settings that they believe are best suited to the new assembly. One dedicated to assemblies that contain sensitive parts and require lower temperatures.One dedicated to densely populated assemblies with elevated temperatures.

The time taken to perfect the baseline profile will pay dividends as most assemblies will then fall within one of them. Over time, some EMS providers may develop a range of "baseline" profiles, which can then be selected depending on the PCBA they are working on. The New Product Introduction ( NPI) engineer will usually start the process by selecting an oven profile they have used before and that is stored on their system. So what should your EMS partner be doing to perfect their reflow oven profile? Let's find out. If you fail to profile the oven correctly, then all of the hard work and effort that has gone into loading feeders, programming the machines, optimising the build and then running the production line will be wasted. The reflow oven is used primarily for the reflow soldering of surface mount electronic components to printed circuit boards (PCB). There is however one specific step that can make all of the difference when it comes to quality and consistency - creating the surface mount (SMT) reflow oven profile. But, broadly speaking, the process steps that they go through to produce PCBAs are the same. But consistently producing them in volume can take time to perfect.Įlectronics manufacturing services (EMS) providers may well have their own preferences when it comes to their choice of machine type and brand. Hence, the optimized relation between the process set-up parameters in the oven, simulated thermal behavior, and the voids fraction in solder material are studied in detail.Printed Circuit Board Assemblies ( PCBAs) are often viewed as commodity items. The void content in the solder material was investigated by the X-Ray analysis and correlated with the thermal process in the simulation. The simulation model can be used to predict the temperature distribution for the solder materials together with the demonstrator board. Moreover, the heat transfer coefficient for each thermal profile has been calculated. A set of experimental tasks were designed to investigate the variations in the temperature profiles at selected points on the surface of the demonstrator. This model considers the effect of the complex boundary conditions during the soldering process. This paper presents a simulation model of the thermal soldering process in the over-pressure convection oven by finite element model. The enhanced reflow soldering oven with an integrated hyper pneumatic module ensures a void-free solder connection, but it requires design and installation of the process parameters in the oven in order to ensure optimized heat transfer and derive the best energy efficiency performance. The advanced technologies for electronics production and convection based soldering technologies are growing steadily.
